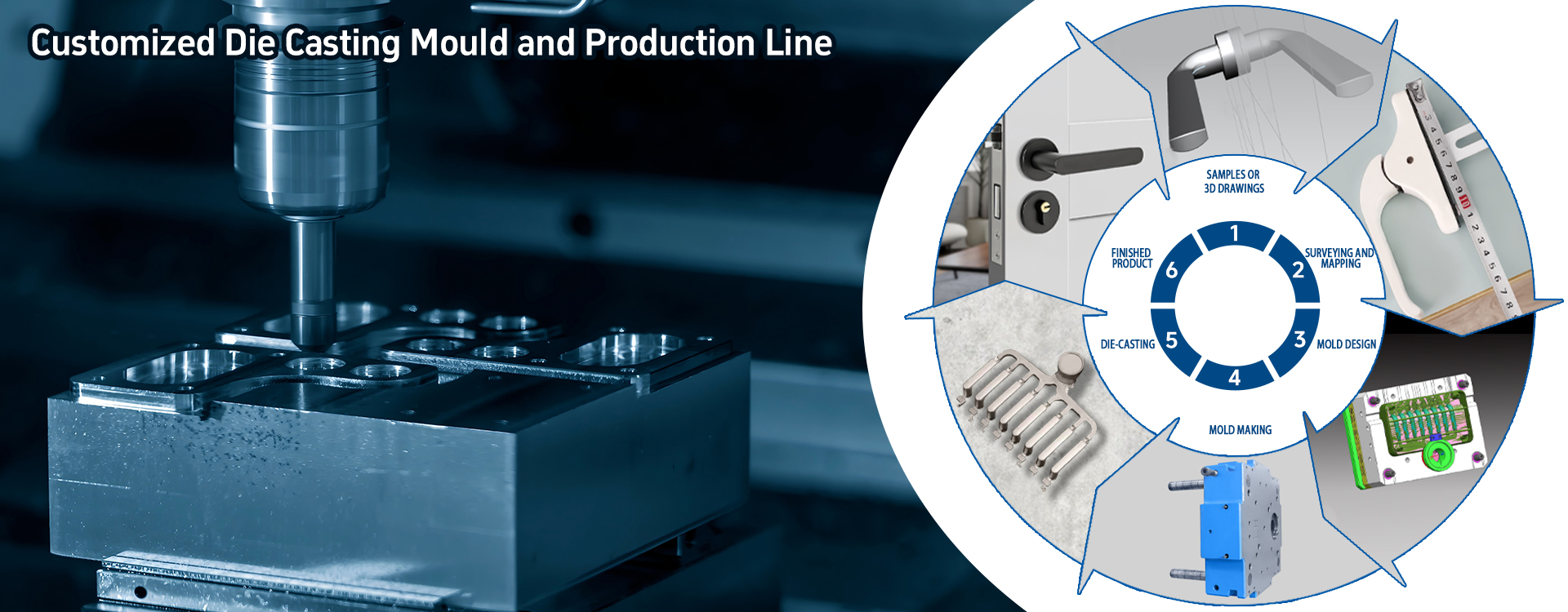
Greetings and welcome to LongHua! We are here to provide you with reliable and dependable solutions for custom die casting mold requirements that are specifically designed to meet your individual specifications and needs. With our expertise as a prominent manufacturer, we focus on creating personalized die casting molds and production lines. Our commitment is to deliver exceptional services and top-quality products to professionals in the industry.
Efficiency and precision with an advanced mechanism for clamping
Our die casting molds are equipped with state-of-the-art clamping mechanisms that are designed to deliver top-notch performance and dependability. The size of the hinges has been calculated using computer optimization techniques, guaranteeing swift running speed and enhanced magnification. Additionally, the utilization of ductile iron and cast steel in the construction of these molds provides a satisfactory level of strength and rigidity, thereby minimizing the likelihood of any untoward breakage during regular operations. Furthermore, the head plate, middle plate, and tail plate have all been reinforced, along with the implementation of a gantry structure, thereby augmenting the overall strength and rigidity of the mold. This meticulous attention to detail ensures that our production processes are carried out with utmost precision and efficiency.
Superior quality achieved through innovative mechanism of injection
Our injection mechanisms are designed with advanced features that guarantee both exceptional quality and efficiency in the casting process. These mechanisms incorporate state-of-the-art external pressure-preserving check valve structures and innovative sealing designs, resulting in seamless integration and minimal failure rates. Moreover, we utilize forgings and special materials like nitrided hot mold steel and carburized and quenched steel to ensure long-lasting durability and unwavering reliability. Additionally, our injection systems boast increased accumulator capacity and precise pressure settings, enabling them to deliver formidable and accurate injections.
Metal Prototypes and On-demand Production: Comprehensive Solutions
Here at LongHua, we provide a wide range of manufacturing services for metal prototypes and on-demand mold production. No matter if you need customized die casting molds for prototypes or high-volume production lines, our team of skilled professionals is committed to delivering creative solutions that match your specific requirements and go beyond your anticipations. With cutting-edge equipment and technology like advanced clamping mechanisms and efficient hydraulic systems, we guarantee accuracy, dependability, and uniformity in every project we undertake.
Come and discover the remarkable distinction that awaits you when you choose LongHua Die Casting Machines. With our steadfast dedication to excellence, ingenuity, and ensuring that our customers are fully content, we become your unparalleled companion in providing tailor-made services for manufacturing die casting molds. Take the initiative today to get in touch with us and delve deeper into understanding how we can effectively assist you with all your requirements for metal prototypes and the production of molds whenever the need arises.
FEATURE GUIDES THAT INTEREST YOU
R&D Capabilities for Custom Die Casting Mold
At LongHua, we take pride in our robust research and development (R&D) capabilities, which are at the forefront of innovation in the field of custom die casting mold manufacturing. Our dedicated R&D team works tirelessly to push the boundaries of technology, ensuring that we stay ahead of the curve and continue to deliver cutting-edge solutions to our clients.
Our R&D efforts focus on enhancing the precision and efficiency of clamping mechanisms through computer-optimized designs and material selection. We conduct thorough analyses to determine the optimal hinge size and configuration, resulting in fast running speeds and magnification ratios ranging from 22 to 25. Through innovative approaches, we ensure that our clamping mechanisms provide the necessary strength and rigidity while minimizing the risk of breakage during normal use.
What Is A Die Casting Mould?
Die casting molds, also known as dies, are specialized tools used in the manufacturing process of die casting. They are designed to shape molten metal into specific geometrical shapes, often with intricate details and high precision. Die casting molds are typically made of hardened steel and are custom-designed to produce parts according to the exact specifications of the final product.
A die casting mold is a specialized tool used in the die casting process to shape molten metal into specific geometrical shapes. It consists of key components such as the cavity, core, sprue, runners, ejector pins, cooling channels, and venting system. Die casting molds are essential for producing high-quality metal parts with precision and consistency, making them indispensable in various industries such as automotive, aerospace, electronics, and more.

How to Make a Die Casting Mould ?
The process of making a die casting mold involves several intricate steps to ensure precision and quality in the final product. Here's an overview of the typical process involved in making a die casting mold:
1. Design and Engineering:
- The first step in making a die casting mold is to create a detailed design based on the specifications of the final product. This involves engineering considerations such as part geometry, material properties, and production requirements.
2. Material Selection:
- Once the design is finalized, the appropriate materials for the mold are selected. Die casting molds are typically made from hardened steel, such as H13 tool steel, due to its high strength and wear resistance.
3. CNC Machining:
- The next step is to use computer numerical control (CNC) machining to fabricate the mold components from the chosen material. CNC machining allows for precise shaping and detailing of the mold cavity, core, sprue, runners, and other features.
4. Heat Treatment:
- After machining, the mold components undergo heat treatment to improve their hardness and durability. Heat treatment processes such as quenching and tempering are commonly used to achieve the desired material properties.
5. Assembly:
- Once the individual components are machined and heat-treated, they are assembled into a complete die casting mold. This involves fitting the cavity and core together, along with any additional components such as ejector pins, cooling channels, and venting systems.
6. Surface Finishing:
- Surface finishing techniques, such as polishing and coating, may be applied to the mold to enhance its performance and prolong its lifespan. These finishing processes help achieve smoother surface finishes on the final castings and reduce the risk of defects.
7. Testing and Validation:
- Before the mold is put into production, it undergoes rigorous testing and validation to ensure its functionality and reliability. This may involve trial runs with simulated casting processes to verify the mold's performance and make any necessary adjustments.
8. Production:
- Once the mold has been tested and approved, it is ready for production. Molten metal is injected into the mold cavity under high pressure, where it solidifies to form the desired part shape. The mold is then opened, and the finished part is ejected, ready for further processing or assembly.
The process of making a die casting mold is a complex and precise undertaking that requires careful planning, engineering expertise, and advanced manufacturing techniques. By following these steps, manufacturers can create high-quality molds that meet the exact specifications of their customers and ensure the production of consistent, reliable castings.
Die Casting Types Available from Longhua
Longhua offers a comprehensive range of die casting types to cater to various industrial needs and applications. With our advanced manufacturing capabilities and expertise, we provide high-quality die casting solutions tailored to meet the specific requirements of our clients. Here are the die casting types available from Longhua:
1. Aluminum Die Casting:
- Aluminum die casting is a versatile process ideal for producing complex parts with high dimensional accuracy and excellent surface finishes. Longhua specializes in aluminum die casting, offering a wide range of aluminum alloys to suit different application needs.
2. Zinc Die Casting:
- Zinc die casting is known for its excellent strength-to-weight ratio, corrosion resistance, and intricate detailing capabilities. Longhua's zinc die casting services deliver high-quality parts suitable for various industries, including automotive, electronics, and consumer goods.
3. Magnesium Die Casting:
- Magnesium die casting offers lightweight yet durable components with excellent thermal conductivity and dimensional stability. Longhua's magnesium die casting capabilities enable the production of lightweight parts for aerospace, automotive, and electronics applications.
4. Brass Die Casting:
- Brass die casting provides superior corrosion resistance, electrical conductivity, and aesthetic appeal, making it suitable for decorative and functional components. Longhua offers brass die casting services for applications in plumbing fixtures, hardware, and electrical connectors.
5. Custom Die Casting Solutions:
- In addition to standard die casting types, Longhua specializes in providing custom die casting solutions tailored to meet the unique requirements of our clients. Our experienced team works closely with customers to develop customized die casting molds and production processes, ensuring optimal performance and cost-effectiveness.
Available Custom Die Casting Finishes
Longhua provides a variety of custom die casting finishes to enhance the appearance, functionality, and durability of your casted parts. Our range of finishes ensures that your components meet your specific aesthetic and performance requirements, catering to diverse industries and applications. Here are the available custom die casting finishes offered by Longhua:
1. Powder Coating:
- Powder coating is a versatile finish that provides excellent durability, corrosion resistance, and aesthetic appeal to die-casted parts. Longhua offers a wide range of powder coating colors and textures to achieve the desired look and feel for your components.
2. Anodizing:
- Anodizing is a process that creates a protective oxide layer on the surface of aluminum die-casted parts, enhancing their corrosion resistance and durability. Longhua offers various anodizing options, including clear, black, colored, and hardcoat anodizing, to meet your specific requirements.
3. Painting:
- Painting is a customizable finish option that allows you to achieve specific colors, gloss levels, and decorative effects on die-casted parts. Longhua provides professional painting services using high-quality paints and finishes to ensure a flawless appearance and long-lasting performance.
4. Electroplating:
- Electroplating is a surface finishing process that deposits a thin layer of metal onto die-casted parts, providing enhanced corrosion resistance, conductivity, and aesthetic appeal. Longhua offers a range of electroplating options, including chrome, nickel, zinc, and gold plating, to suit various applications and preferences.
5. Polishing and Buffing:
- Polishing and buffing are finishing techniques that create smooth, reflective surfaces on die-casted parts, enhancing their appearance and tactile feel. Longhua's skilled craftsmen use advanced polishing equipment and techniques to achieve the desired finish and surface quality for your components.
6. Shot Blasting:
- Shot blasting is a surface treatment process that removes surface impurities and imperfections from die-casted parts, leaving behind a clean, uniform finish. Longhua offers shot blasting services using various media types and blasting intensities to achieve the desired surface texture and appearance.
7. Custom Finishing Solutions:
- In addition to standard finishes, Longhua specializes in providing custom finishing solutions tailored to meet your unique requirements. Whether you need specialized coatings, textures, or decorative effects, our experienced team can work with you to develop customized finishing solutions that meet your specific needs and preferences.
Advantages of Custom Die Casting Mold
Custom die casting molds offer numerous benefits that make them an ideal choice for manufacturing metal parts in various industries. Longhua specializes in providing custom die casting mold solutions tailored to meet the specific needs and requirements of our clients. Here are the key advantages of choosing custom die casting molds from Longhua:
1. Precision and Consistency:
- Custom die casting molds are engineered with precision to produce parts with tight tolerances and consistent dimensions. Longhua's advanced manufacturing processes ensure that each mold is meticulously designed and fabricated to meet the exact specifications of the final product, resulting in high-quality, uniform parts.
2. Versatility and Flexibility:
- Custom die casting molds offer versatility and flexibility in design, allowing for the production of complex parts with intricate details and unique geometries. Longhua's experienced engineers work closely with clients to develop customized mold designs that meet their specific requirements, enabling greater design freedom and innovation.
3. Cost-effectiveness:
- Custom die casting molds can help optimize production costs by minimizing material waste, reducing secondary operations, and streamlining manufacturing processes. Longhua's efficient design and manufacturing capabilities enable us to deliver cost-effective solutions that meet our clients' budgetary constraints without compromising on quality or performance.
4. Faster Time-to-Market:
- Custom die casting molds can accelerate the product development cycle and shorten time-to-market for new products. Longhua's rapid prototyping and iterative design processes allow for quick turnaround times, enabling clients to bring their products to market faster and gain a competitive edge.
5. Superior Quality and Performance:
- Custom die casting molds manufactured by Longhua are built to the highest quality standards, ensuring superior performance, durability, and reliability. Our rigorous quality control measures and advanced testing procedures ensure that each mold meets or exceeds industry standards, delivering consistent, high-quality parts with every production run.
6. Enhanced Design Capabilities:
- Custom die casting molds offer enhanced design capabilities, allowing for the integration of features such as undercuts, thin walls, and complex geometries. Longhua's team of experienced engineers and designers leverage the latest CAD/CAM software and advanced manufacturing technologies to optimize mold designs for maximum efficiency and performance.
7. Tailored Solutions for Unique Requirements:
- Custom die casting molds enable tailored solutions for unique requirements and specifications. Whether it's a specialized material, surface finish, or dimensional requirement, Longhua works closely with clients to develop customized mold designs that meet their specific needs, ensuring optimal performance and satisfaction.
Custom die casting molds offer numerous advantages, including precision, versatility, cost-effectiveness, faster time-to-market, superior quality, enhanced design capabilities, and tailored solutions for unique requirements. Longhua's expertise in custom die casting mold manufacturing ensures that clients receive high-quality, reliable, and cost-effective solutions that meet their specific needs and exceed their expectations. Contact us today to learn more about our custom die casting mold services and how we can support your project needs.
Customized Die Casting Mould and Production Line Solutions
Longhua offers comprehensive customized die casting mould and production line solutions tailored to the specific requirements of our clients. With our expertise in die casting technology and manufacturing processes, we provide end-to-end solutions that optimize efficiency, quality, and cost-effectiveness. Here's an overview of our customized die casting mould and production line solutions:
Custom Die Casting Mould Design and Development:
Our experienced team of engineers collaborates closely with clients to design and develop custom die casting moulds that meet their unique specifications and requirements. We leverage advanced CAD/CAM software and simulation tools to optimize mould designs for maximum efficiency, precision, and durability.
Precision Die Casting Mould Manufacturing:
Longhua's state-of-the-art manufacturing facilities are equipped with advanced machinery and technology for precision die casting mould manufacturing. We utilize high-quality materials and cutting-edge manufacturing processes to ensure the highest standards of quality and performance in every mould we produce.
Prototype Development and Testing:
Prior to full-scale production, we offer prototype development and testing services to validate mould designs and optimize production processes. Our rapid prototyping capabilities allow for quick iteration and refinement of designs, ensuring optimal performance and reliability in the final production phase.
Customized Production Line Integration:
In addition to die casting moulds, Longhua provides customized production line integration services to streamline manufacturing processes and maximize productivity. We design and implement production lines tailored to our clients' specific needs, incorporating automation, robotics, and advanced control systems for efficient and cost-effective production.
Comprehensive Technical Support and Training:
We provide comprehensive technical support and training to our clients to ensure smooth integration and operation of die casting moulds and production lines. Our team offers training programs tailored to the specific needs of operators, maintenance personnel, and production managers, enabling them to maximize the performance and lifespan of their equipment.
Buyer's Guide
Are you in the market for customized die casting moulds and production line solutions? Longhua is your trusted partner, offering a comprehensive guide to help you navigate the process of choosing the right supplier and optimizing your die casting operations.
1. Define Your Requirements:
Clearly outline your specific requirements for die casting moulds and production line solutions. Consider factors such as production volume, part complexity, and material specifications. This initial assessment will guide your discussions with potential suppliers.
2. Explore Longhua's Expertise:
Longhua specializes in die casting technology, providing extensive expertise in mould design, manufacturing, and production line integration. Our dedicated team of engineers ensures that your customized solutions meet the highest standards of precision and efficiency.
3. Cutting-Edge Technology at Longhua:
Longhua boasts state-of-the-art manufacturing facilities equipped with advanced machinery, CAD/CAM software, and simulation tools. Our commitment to technology ensures that your die casting moulds and production lines are at the forefront of industry standards.
4. Rapid Prototyping Services:
Longhua offers rapid prototyping services to validate mould designs and optimize production processes swiftly. Our prototyping capabilities allow for quick iteration, ensuring that the final production phase meets your expectations for efficiency and reliability.
5. Tailored Production Line Integration:
Longhua excels in designing and implementing customized production lines. Our solutions are tailored to your specific needs, incorporating automation, robotics, and advanced control systems for maximum efficiency and productivity in your die casting operations.
6. Stringent Quality Assurance by Longhua:
Quality is paramount at Longhua. Our comprehensive quality control measures ensure that your die casting moulds and production lines meet or exceed industry standards. We prioritize the delivery of products and processes that consistently meet customer expectations.
7. Comprehensive Technical Support:
Longhua provides comprehensive technical support and training to ensure seamless integration and operation of your die casting equipment. Our training programs are tailored to the specific needs of operators, maintenance personnel, and production managers.
8. Success Stories and References:
Longhua proudly shares success stories and references from past projects similar to yours. Explore our track record to gain insight into our capabilities, reliability, and customer satisfaction levels.
9. Negotiate Transparently with Longhua:
Engage in transparent negotiations with Longhua. Our team is committed to clarity in pricing and terms, ensuring a mutually beneficial partnership. Understand the costs involved, including tooling, production, and any additional services required.
10. Contact Longhua Today:
Ready to optimize your die casting operations? Contact Longhua today to discuss your requirements. Our team is here to guide you through the process, providing unmatched expertise, cutting-edge technology, and a commitment to excellence in die casting solutions.
Choose Longhua for a seamless and efficient experience in obtaining customized die casting moulds and production line solutions. We look forward to partnering with you for success in your manufacturing endeavors.
Why Should You Choose LongHua for Custom Die Casting Mold?
- State-of-the-art manufacturing facilities equipped with advanced machinery and technology.
- Extensive experience and expertise in die casting processes and materials.
- Comprehensive quality control measures to ensure the highest standards of product quality and consistency.
- Dedicated customer support and technical assistance throughout the entire die casting process.
- Commitment to innovation, sustainability, and continuous improvement in die casting technologies and practices.
Custom Die Casting Mold Cost
Investing in a custom die casting mold involves considerations beyond the initial purchase price. The cost-effectiveness of the mold is determined by its performance, durability, and efficiency. Let's delve into key aspects of the clamping mechanism, injection mechanism, hydraulic system, and machine base to understand how these factors contribute to the overall cost of a custom die casting mold.
1. Clamping Mechanism:
- Size and Speed: Computer-optimized design ensures the machine hinge size is calculated for optimal performance, running at a fast speed with a magnification of 22-25.
- Material Choice: Ductile iron (cast steel) provides a balanced combination of strength and rigidity, minimizing the risk of breakage during regular use.
- Reinforced Structure: Thickened head, middle, and tail plates with a gantry structure enhance stencil strength and rigidity.
- Ejector Cylinder: Double cylinder (single cylinder) external mode with guided pillars minimizes maintenance issues.
- Crank Arm Design: Six shear plane design and lengthened crank arm pin with card-type positioning for balanced force and durability.
- Material Quality: Nitriding of hot mold steel (38CrMoAl) for the crank pin ensures superior hardness and extended service life.
- Crank Arm Sleeve: 20Cr carburizing and quenching with surface hardness above HRC60 for increased durability.
- Mold-Adjusting Nut: Ductile iron (QT500-7) ensures smooth and fast mold adjustments.
2. Injection Mechanism:
- Pressure-Preserving Check Valve: External structure with high integration and low failure rate for enhanced reliability.
- Injection Cylinder: Processed by forgings to guarantee wear resistance.
- Unique Sealing Structure: Injection piston rod with a sealing structure that prevents oil seepage or leakage.
- Enhanced Accumulator: Increased total capacity for more powerful injections.
- Accumulator Pressure Control: Set by the fast accumulator and supercharge accumulator for precise control.
- Accumulator Piston Seal: Special gas seal + oil seal structure for optimal performance.
3. Hydraulic System:
- Double Pump Configuration: High and low pressure double pump configuration for energy-efficient system power.
- Compact Valve Block: Two structures for injection and pressure valve block, ensuring a compact and simple layout.
- Mode-Locking Principle: Unique mode-locking principle for fast clamping and mold opening speed.
- Leak-Proof Seals: Hydraulic hoses and joints sealed with German standard 24° cones to prevent leaks.
- Compact Layout: Few piping and highly integrated valve blocks contribute to a compact and efficient hydraulic system.
4. Machine Base:
- Forged Guide Rail: Processed by forgings, the guide rail offers high strength, good rigidity, and minimal wear.
- Shot Peening: Interior shot peening removes residues such as rust and welding slag, ensuring a clean hydraulic system.
Understanding the components and features of a custom die casting mold, such as the clamping mechanism, injection mechanism, hydraulic system, and machine base, is essential in evaluating the overall cost. Longhua's commitment to quality materials, precision engineering, and advanced technology ensures that your investment in a custom die casting mold is optimized for performance, durability, and efficiency. Contact Longhua today to explore how our expertise can contribute to the success of your die casting operations.
What Our Customers Say?
Takashi Yamamoto
We chose Longhua for their reputation in the industry, and they delivered beyond our expectations. The clamping mechanisms and injection systems in our customized die casting molds have significantly improved our production processes, resulting in higher yields and reduced downtime.
Get an Online Quote and Die Casting Mold Design Analysis Today
Ready to elevate your manufacturing processes with precision die casting molds? Take the first step towards excellence by obtaining an online quote and a comprehensive design analysis for your custom mold needs. Our team at Longhua is here to provide you with tailored solutions that optimize performance and efficiency. Start the journey to enhanced manufacturing capabilities – get your quote and analysis today!